3D printed bike saddle has become a new trend. But is it really worth buying? 3D printed saddles are manufactured using 3D printing technology and typically use high-performance materials such as nylon, carbon fiber-reinforced composites, or thermoplastic polyurethane, offering more customization options and high-performance advantages. Overall, compared to traditional road bike saddles, 3D printed saddles are stronger in performance, lighter in weight, easier to maintain, more reliable, and support quick customization. While the price might be higher, they are definitely worth it.
3D Printed Bike Saddle: More Precise Mechanical Support
Another point worth mentioning is that if you’ve purchased traditional road bike saddles, you’ll notice they are divided into 4-6 zones. Different areas use different materials and structural designs to reduce weight while making your ride more comfortable. Due to limitations in the precision of traditional production equipment, manufacturers can at most divide the saddle into 10 zones, each redesigned separately. However, a 3D printed bike saddle can have thousands of such zones. By designing the shape, structure, and fiber thickness of the filling materials in each sub-unit, the entire saddle can achieve the desired mechanical properties, even allowing customization for each rider. Simply put, 3D printing can make the hard areas hard, the soft areas soft, and the elastic areas have good elasticity.
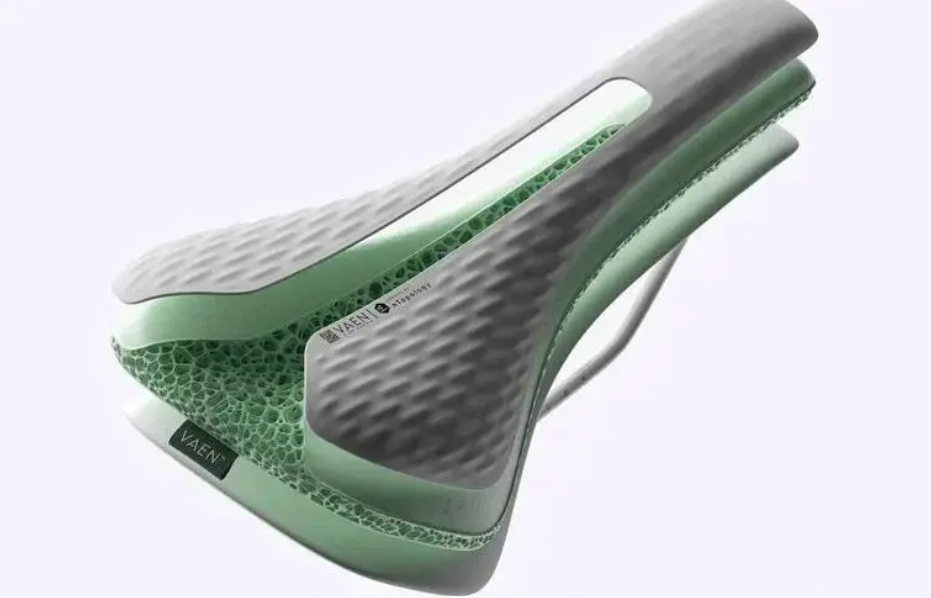
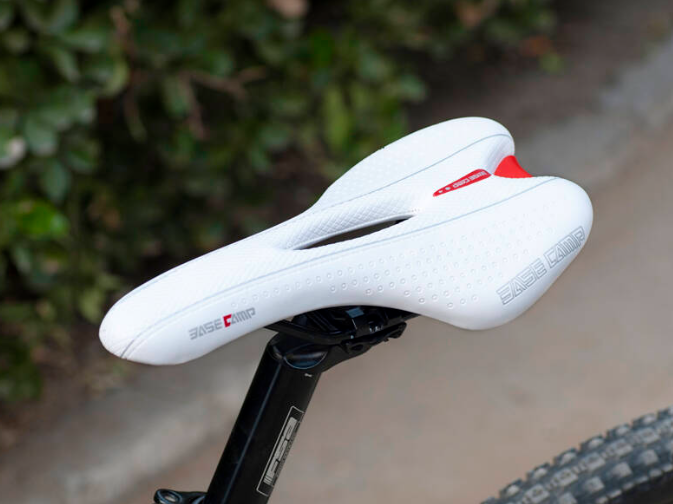
3D Printed Bike Saddle: Breathability and Lighter Weight
3D printing inherently produces a hollow material, giving it excellent breathability. Traditional road bike saddles need special designs, such as reserved airways, to enhance breathability. However, the breathability from a few holes and airways in traditional designs pales in comparison to the inherent breathability of a 3D printed bike saddle without any special structural design. Since 3D printed saddles are generally hollow, they are usually very light, typically weighing between 100-250 grams.
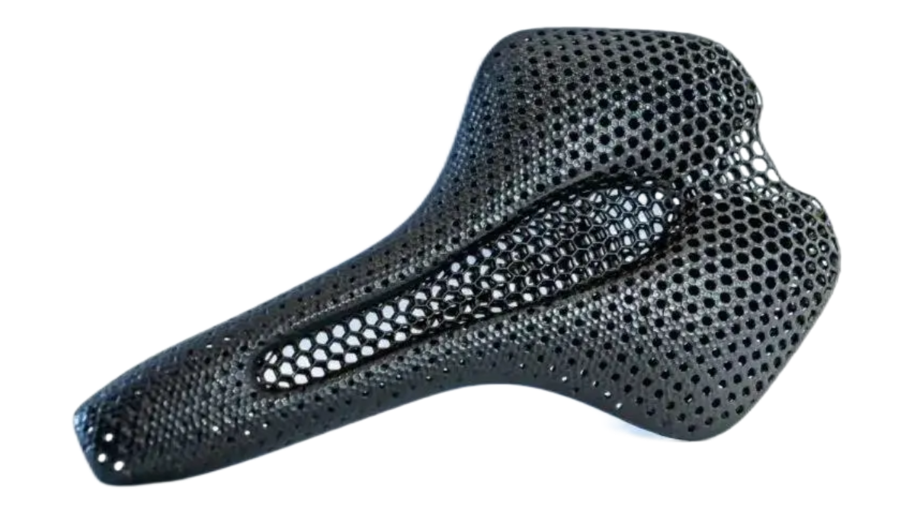
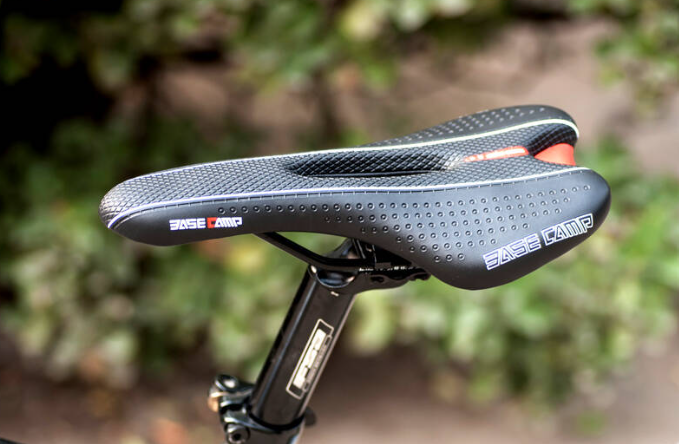
More Reliable and Easy to Maintain
When a traditional road bike saddle develops a small tear, this damage often worsens over time. However, if a 3D printed saddle suffers a small tear, the damaged structural unit is relatively independent, and the surrounding units can still provide good support. The independence among thousands of structural units is very strong. In most cases, 3D printed bike saddles are made of TPU and carbon fiber, meaning you only need to rinse them with water for cleaning without worrying about sponge water absorption or metal rusting.
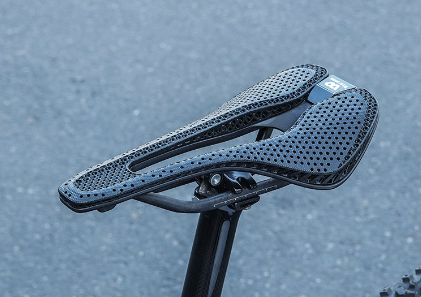
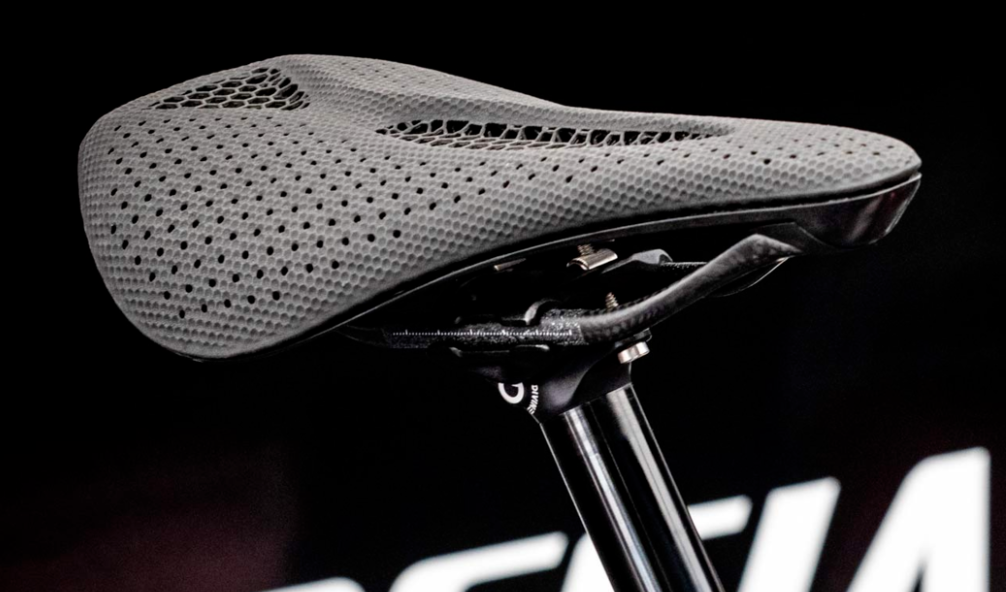
Benefits for Both Consumers and Manufacturers
Not only do consumers love it, but producers also favor them because computers can complete a new saddle design and testing processes, making it more efficient. In terms of environmental protection, 3D printed bike saddles can significantly reduce waste during manufacturing, and some materials are recyclable. These advantages make 3D printed saddles increasingly popular in the high-end bicycle market, especially in professional racing and long-distance cycling, which require high-performance equipment.
By the way, SUMLON has been manufacturing bicycle parts for over 15 years. Contact us if you are looking for a bike parts factory or a one-stop wholesaler. Peace